The Cable Bus Advantage
Reliable, Fail-Safe Power
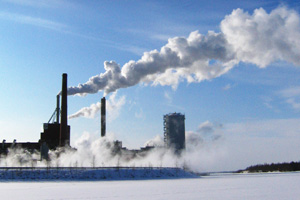
For over five decades, Cable Bus has demonstrated its superior reliability in the power generation, mining, petrochemical, paper, heavy industrial and commercial industries. It functions beautifully in conditions ranging from heavy pollution to extremes of temperature, humidity and UV light, from humid tropics to hot, dry deserts and frozen tundras. Advanced Cable Bus systems are custom-engineered to operate in any climate, anywhere in the world.
Cost-Effective & Energy Efficient
With material and installation costs of up to 40% in comparison to conventional, non-segregated phase bar bus, cable tray with armored cables, or conduit and wire systems, Cable Bus is often the most cost-effective way of distributing electricity.
Learn more... about the savings you'll experience with an Advanced Cable Bus system.
Flexible & Versatile
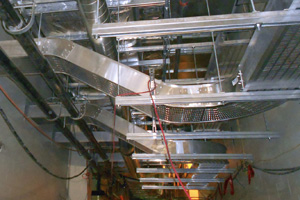
We take pride in providing the most accurately designed and manufactured systems on the market. However, during the course of a project, unexpected circumstances can occur. In order to keep the project on track and avoid delays, all our systems are furnished with an extra housing section that can be cut to fit if the need arises. The power cables we supply also include a complimentary 5% in additional length to accomodate any discrepancies encountered in the field.
Learn more... about customizing your Advanced Cable Bus system.
Easy to Install
Advanced Cable Bus systems are easy to install compared to other systems. No heavy lifting equipment or special tools are required; housing sections can easily be lifted into place by two men.
Every job is engineered and designed to fit the specific application with all Cable Bus sections, elbows and accessories factory pre-cut to fit your project needs. Long vertical sections are easily installed using our Short Circuit Braces, which allow the Cable Support Blocks to be installed without any fasteners until all the power cables have been pulled into place. Interleaving or crossing of conductors within the Cable Bus enclosure is not required with our systems.
Maintenance-Free
Advanced Cable Bus systems are completely maintenance-free. Unlike traditional, non-segregated phase bus duct systems, there are no splices, no connections to re-torque, and no space heaters or thermostats to install or replace.
The ADV motto is: "Install it, power up, and forget it!"
Cable Bus vs. Alternatives
Cable Bus is a competitive alternative to conventional,
non-segregated phase bar bus, cable tray
with armored cable, and conduit and wire systems.
This is because of its lower cost, higher reliability,
greater flexibility, easier installation and longer life expectancy.
Ampacity Comparison
Cable Bus vs. the Field
greater flexibility, easier installation and longer life expectancy.
Ampacity Comparison
Cable Bus vs. the Field
System Rating | Conductor Size | Advanced Cable Bus Systems | Interlocked, Armored Cable in Tray | 3, Single-Conductor Cables in Conduit/Air |
---|---|---|---|---|
600V | 500 MCM 750 MCM 1000 MCM |
637 Amps 805 Amps 960 Amps |
405 Amps 500 Amps 585 Amps |
477 Amps 598 Amps 689 Amps |
5kV | 500 MCM 750 MCM 1000 MCM |
688 Amps 889 Amps 1,061 Amps |
425 Amps 525 Amps 590 Amps |
473 Amps 579 Amps 659 Amps |
15kV | 500 MCM 750 MCM 1000 MCM |
678 Amps 872 Amps 1,040 Amps |
470 Amps 570 Amps 650 Amps |
481 Amps 588 Amps 677 Amps |
The cost of conductors for cable bus will be lower than others, and that is mainly due to the ability to use free air rating. And the installation costs will be comparable to cables in tray of the same size, the only difference being that we use support blocks and a top cover, whereas cable in tray will require fasteners to keep the cables and maintain position in many cases, as well as cables in tray requiring larger amount of cable for the same current rating.
The cost of enclosures for cable bus is high in relation to cables in tray and cables in conduit, because the other types are basically bulk material that ordered quite conveniently, whereas cable bus is an engineered system, very similar to bus duct.
Cable bus has a further advantage of being the only type of installation where the manufacturer's design guarantees that the conductor current will be as balanced as it can be. And the other advantage for cable bus is that it has flexibility in routing and design, again similar to cable tray, where we ship bottom sections, and we fabricate our own elbows, therefore we can go at any odd angle that's required. Cable bus can still work with hinged splice plates, if necessary. And also, every project that Advanced Cable Bus supplies will come with excess cables, free of charge, as well as spare enclosure parts, free of charge, in order to account for any minor variations in the field.
When you compare the common voltage classes that can be applied for the various methods of distribution feeder, cable bus is comparable to all, where it can be used for medium voltage as well as low voltage. And the current levels for cable bus can also be designed up to 5,000 amps and higher, which is comparable to bus ducts as well as cables in conduits.
And the enclosure size is where the cable bus advantage begins to pull away from the pack, where the maximum size for cable bus, so far, has been 26 inches wide by 12 inches high. And for a comparable rated bus duct, that size is usually up to 36 inches by 18. And cables in tray, if you go up to 5,000 amps, you will end up with multiple tray runs. And cables in conduit will also eat up quite a bit of air space.
The fault current that the system can withstand, for cable bus, is tested to the same standard as bus ducts, and therefore these two methods have comparable fault current withstand capabilities, whereas cables in tray and cables in conduit will have to require special cable cleats, or special installation techniques, in order to allow that to happen.
Cable bus is also comparable to bus ducts in that the cable bus designed phase will include engineering drawings, as well as engineering calculations of the electrical property of the finished run. In other words, the strength, durability, and reliability of Cable Bus systems are similar to those of rigid bus ducts, but Cable Bus systems are more compact and physically flexible.
Typical Applications
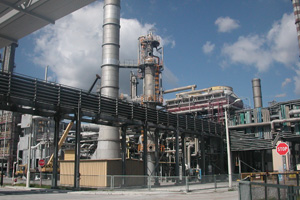
Main Incoming & Distribution Feeders
These include main feeders to facilities, whether they're medium or low voltage systems. These include feeders at industrial plants, mining and metal facilities, oil & gas and oil sands facilities, data center facilities, and UPS feeds.
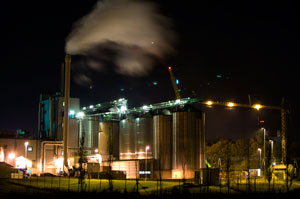
Power Generation Plants
Cable bus can be used as main generation feeds, station service feeds, auxiliary feeds, and excitation feeds.
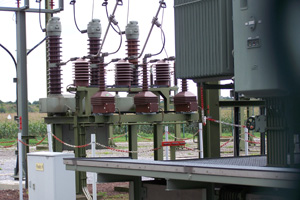
Power Distribution Substations
For many utilities, cable bus is the preferred choice for feeders connecting the power transformers' LV terminals to the switchgear lineups before the power gets distributed to the distribution circuits.
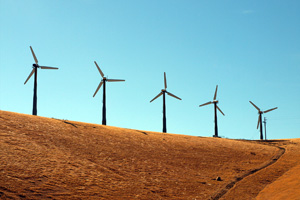
Renewable Energy Solutions
Solar Plant collector substation links between collector transformers and switchgears.
Solutions by Industry
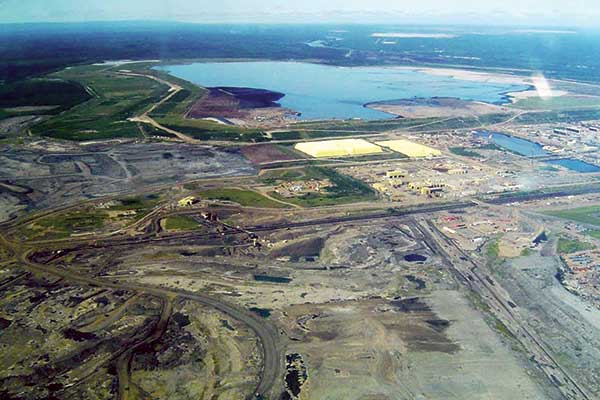
Oil, Oil Sands & Gas
Historically cable bus has been used at extraction plants, refineries, processing plants, and distribution plants everywhere from the Middle East to Texas to South America to the Arctic.
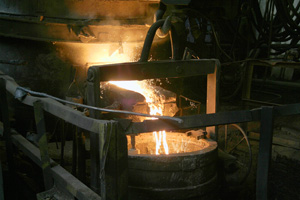
Mining & Metals
Because of flexibility and reliability, cable bus makes a great fit for projects where there may be uncertainty in jobsite final dimensions. The low losses and balanced line parameters result in better voltage drops and power quality.
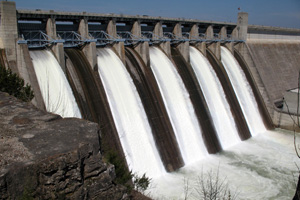
Electrical Utilities
Applications for electric utilities include generator main power feeds, station service feeds, FGD feeds, auxiliary feeds, and excitation system feeds.
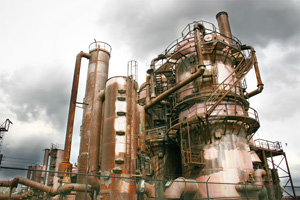
Industrial Loads
Cable bus provides economical options for a wide range of voltage and current ratings, especially for main distribution or industrial load feeders.
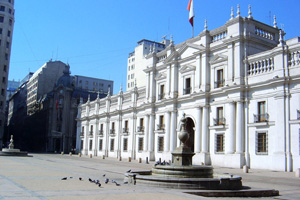
Public Buildings
Cable bus's flexibility allows for feeder designs to fit into a wide range of building design aesthetics and follow odd routes at smaller cross-sections than other types of feeders.